CALL US: 406-253-3161

AGNES
THE ANANGAMA KILN
Wood-fired kilns are an ancient science. Several centuries ago, far-eastern potters began to build wood-fired tunnel kilns known as Anagamas. The kilns were built on hillsides; exploiting the natural slope to help create a draw in the kiln. These types of kilns are fired anywhere between 2 days and 3 weeks. Our firings have varied between 3 1/2 to 5 days.
The Anagama kiln at Whitefish Pottery, affectionately known as Agnes (after Tom’s Great Aunt), can hold approximately 1500 pots and takes about 24 hours to load. To start, a small fire is lit in the mouth of the kiln. Constant attention is given to the fire, slowly increasing the kilns temperature. Gradually, as the temperature rises to 2400oF, the kilns appetite grows along with the pace in which wood is fed into the kiln. Potters and other contributors from throughout the valley work together in rotating shifts to constantly feed Agnes’ hunger for wood.
The flame from the firebox will travel through the entire length of the kiln (in this case, about 50 feet) to billow out the chimney during the peak of the firing. The flames maneuver around the pottery inside creating an effect known as flashing. The nature in which the flame moves through the kiln is uncontrollable. During this period, fly-ash carried by the flames from the firebox settles on the pottery and begins to melt, coating the ware with a natural occurring ash glaze.
Pottery fired in this manner is unique and no two are ever alike.
Call us if you are interested in firing with us. We typically fire in late May. 406-253-3161

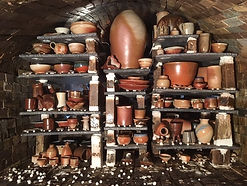

The firing starts off slow and steady with a small "campfire" and propane to get her going, then we move on to fueling with wood that has been cut and stacked in preparation for the firing.
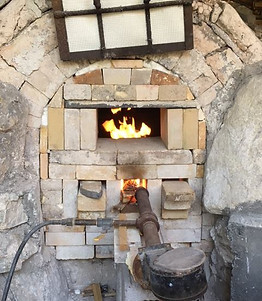
The firing starts off slow and steady with a small "campfire" and propane to get her going, then we move on to fueling with wood that has been cut and stacked in preparation for the firing.

Each pot has "wads" (those little clay balls on the left) gently attached to them so that they do not touch the shelf directly. These wads leave distinctive marks on the finished pots.